Dabadger84
CLASSIFIED Member
- Total Posts : 3426
- Reward points : 0
- Joined: 2018/05/11 23:49:52
- Location: de_Overpass, USA
- Status: offline
- Ribbons : 10

Re: 3090 (Kingpin & others!) - Get that backside VRAM cool!
2021/02/27 22:11:47
(permalink)
Does anyone know a good place that doesn't overcharge to purchase Fujipoly thermal pads from? I'm trying to get ahold of some of their 17W/mK stuff just to redo the VRAM on the backplate side (and possibly redo the face side later with it). Since that's the area that puts out the most heat according to temperature readouts, I figure upgrading pads on there would be best. If I can't find that, I'll just order another thing of the 12W/mK stuff & redo the 2 areas of the VRAM I haven't done yet with that (the two 4-chip blocks).
ModRigs: https://www.modsrigs.com/detail.aspx?BuildID=42891 Specs:5950x @ 4.7GHz 1.3V - Asus Crosshair VIII Hero - eVGA 1200W P2 - 4x8GB G.Skill Trident Z Royal Silver @ 3800 CL14Gigabyte RTX 4090 Gaming OC w/ Core: 2850MHz @ 1000mV, Mem: +1500MHz - Samsung Odyssey G9 49" Super-Ultrawide 240Hz Monitor
|
Dabadger84
CLASSIFIED Member
- Total Posts : 3426
- Reward points : 0
- Joined: 2018/05/11 23:49:52
- Location: de_Overpass, USA
- Status: offline
- Ribbons : 10

Re: 3090 (Kingpin & others!) - Get that backside VRAM cool!
2021/02/27 23:50:06
(permalink)
 I've gone off the deep end. BTW covering this area with a fairly thin layer took an entire 1.5ml syringe of thermal grizzly - rip $15 if this sucks. Edit: it did not suck, see below results.
post edited by Dabadger84 - 2021/02/28 01:00:48
ModRigs: https://www.modsrigs.com/detail.aspx?BuildID=42891 Specs:5950x @ 4.7GHz 1.3V - Asus Crosshair VIII Hero - eVGA 1200W P2 - 4x8GB G.Skill Trident Z Royal Silver @ 3800 CL14Gigabyte RTX 4090 Gaming OC w/ Core: 2850MHz @ 1000mV, Mem: +1500MHz - Samsung Odyssey G9 49" Super-Ultrawide 240Hz Monitor
|
Dabadger84
CLASSIFIED Member
- Total Posts : 3426
- Reward points : 0
- Joined: 2018/05/11 23:49:52
- Location: de_Overpass, USA
- Status: offline
- Ribbons : 10

Re: 3090 (Kingpin & others!) - Get that backside VRAM cool!
2021/02/28 00:01:36
(permalink)
Test still has a long way to go but normally I'm already at 68C junction by now. Pic attached cuz I'm on mobile. Edit: BTW the labels are kind of wrong. It's Mem1 Mem2 Mem3 junction on the first temp line, pwr 1-5 on the second. VR loop stuff is motherboard VRM readouts. Edit 2: I really hope this is effective because cleaning that off will be a serious pain in the rear. So far so good though. Mems are at 45-53-46, junction is peaking at 66 but bubbling down to 64 a lot, and VRMs appear to have Leveled off. Note the only VRM with paste over it is the lower one, upper/port side of the card is still thermal tape. Think I'm over halfway in now.
post edited by Dabadger84 - 2021/02/28 00:07:59
Attached Image(s)
ModRigs: https://www.modsrigs.com/detail.aspx?BuildID=42891 Specs:5950x @ 4.7GHz 1.3V - Asus Crosshair VIII Hero - eVGA 1200W P2 - 4x8GB G.Skill Trident Z Royal Silver @ 3800 CL14Gigabyte RTX 4090 Gaming OC w/ Core: 2850MHz @ 1000mV, Mem: +1500MHz - Samsung Odyssey G9 49" Super-Ultrawide 240Hz Monitor
|
Dabadger84
CLASSIFIED Member
- Total Posts : 3426
- Reward points : 0
- Joined: 2018/05/11 23:49:52
- Location: de_Overpass, USA
- Status: offline
- Ribbons : 10

Re: 3090 (Kingpin & others!) - Get that backside VRAM cool!
2021/02/28 00:25:28
(permalink)
Think these are going to be my peaks. Edit: darn, it actually it 68C junction temp. I think changing pads to higher conductivity ones to match the paste better would help even more. Funny I'm getting as good or better Temps than direct pad to heatsink contact though. Was this worth the entire tube of paste? We'll see once I get better pads under the plate.
post edited by Dabadger84 - 2021/02/28 00:30:40
Attached Image(s)
ModRigs: https://www.modsrigs.com/detail.aspx?BuildID=42891 Specs:5950x @ 4.7GHz 1.3V - Asus Crosshair VIII Hero - eVGA 1200W P2 - 4x8GB G.Skill Trident Z Royal Silver @ 3800 CL14Gigabyte RTX 4090 Gaming OC w/ Core: 2850MHz @ 1000mV, Mem: +1500MHz - Samsung Odyssey G9 49" Super-Ultrawide 240Hz Monitor
|
Dabadger84
CLASSIFIED Member
- Total Posts : 3426
- Reward points : 0
- Joined: 2018/05/11 23:49:52
- Location: de_Overpass, USA
- Status: offline
- Ribbons : 10

Re: 3090 (Kingpin & others!) - Get that backside VRAM cool!
2021/02/28 01:00:04
(permalink)
I'm gonna say the thermal paste is definitely doing very positive things, and that if I had the 12.8W/mK thermal pads on ALL of the memory on both sides of the card, it would probably be running even cooler. Right now half the memory on the backplate side of the card is still on 6W/mK Aiyunni pads, and I don't know what eVGA uses for stock pads on the face side, but who knows what the contact is like on that side either. Junction peaked at 68C a few times towards the end of the test, but it was at 64-66C for a good majority of the test. I still think the reason I have a junction that high is that a face-side chip has bad contact, but I have no way of knowing for sure. I'm hoping if I get the 12+W/mK pads on all the memory on the backside, it will help with that, but we'll see. That would be another $30 in pads, and I've already spent something stupid like $100 on JUST thermal pads at this point, including 3mm stuff I have not actually used at all yet :-D But, for easier comparison, here's just the maximum numbers side by side by side: That 14.8C drop on the Mem1 though :-D I have thought about getting Fujipoly again, but because I can't find 2mm pads from them, I'd have to order double what I need in 1mm and that would get expensive fast. Not to mention apparently Fuji extreme has 17W/mK but Thermal Grizzly Kryonaut is only around 12W/mK - so in theory, doing the cheaper 12W pads should be about as good as it's gonna get. I'm just glad I apparently done need to clean that paste off... at least not anytime soon. I would say the paste isn't totally worth it overall, but that 2.5C drop on Mem1 from pads to paste, without all the memory even having the higher quality pads on it, is pretty good... and, as some have pointed out, doing paste makes the heatsinks very much less likely to move around, vs pads (though tape is best, it also performs thermally the worst). I should've included the taped heatsinks only numbers in those charts. Ah well.
ModRigs: https://www.modsrigs.com/detail.aspx?BuildID=42891 Specs:5950x @ 4.7GHz 1.3V - Asus Crosshair VIII Hero - eVGA 1200W P2 - 4x8GB G.Skill Trident Z Royal Silver @ 3800 CL14Gigabyte RTX 4090 Gaming OC w/ Core: 2850MHz @ 1000mV, Mem: +1500MHz - Samsung Odyssey G9 49" Super-Ultrawide 240Hz Monitor
|
DZelmer
Superclocked Member
- Total Posts : 219
- Reward points : 0
- Joined: 2014/11/06 00:37:01
- Status: offline
- Ribbons : 0
Re: 3090 (Kingpin & others!) - Get that backside VRAM cool!
2021/02/28 01:06:19
(permalink)
Do any of you have a 3090 along with the kingpin? if so do the back plates have the screw holes in the same spots?
|
Dabadger84
CLASSIFIED Member
- Total Posts : 3426
- Reward points : 0
- Joined: 2018/05/11 23:49:52
- Location: de_Overpass, USA
- Status: offline
- Ribbons : 10

Re: 3090 (Kingpin & others!) - Get that backside VRAM cool!
2021/02/28 01:14:54
(permalink)
DZelmer Do any of you have a 3090 along with the kingpin? if so do the back plates have the screw holes in the same spots?
I had a 3090 FTW3 Hybrid, past tense, let me see if I can find a good shot of the backside of the GPU, mayhaps I can verify if the screw holes match... Edit: Nope, because of the OLED display, they are different. Here's a shot of the HydroCopper version: vs Kingpin:
post edited by Dabadger84 - 2021/02/28 01:17:59
ModRigs: https://www.modsrigs.com/detail.aspx?BuildID=42891 Specs:5950x @ 4.7GHz 1.3V - Asus Crosshair VIII Hero - eVGA 1200W P2 - 4x8GB G.Skill Trident Z Royal Silver @ 3800 CL14Gigabyte RTX 4090 Gaming OC w/ Core: 2850MHz @ 1000mV, Mem: +1500MHz - Samsung Odyssey G9 49" Super-Ultrawide 240Hz Monitor
|
DZelmer
Superclocked Member
- Total Posts : 219
- Reward points : 0
- Joined: 2014/11/06 00:37:01
- Status: offline
- Ribbons : 0
Re: 3090 (Kingpin & others!) - Get that backside VRAM cool!
2021/02/28 01:18:56
(permalink)
Dabadger84
 I'm gonna say the thermal paste is definitely doing very positive things, and that if I had the 12.8W/mK thermal pads on ALL of the memory on both sides of the card, it would probably be running even cooler. Right now half the memory on the backplate side of the card is still on 6W/mK Aiyunni pads, and I don't know what eVGA uses for stock pads on the face side, but who knows what the contact is like on that side either. Junction peaked at 68C a few times towards the end of the test, but it was at 64-66C for a good majority of the test. I still think the reason I have a junction that high is that a face-side chip has bad contact, but I have no way of knowing for sure. I'm hoping if I get the 12+W/mK pads on all the memory on the backside, it will help with that, but we'll see. That would be another $30 in pads, and I've already spent something stupid like $100 on JUST thermal pads at this point, including 3mm stuff I have not actually used at all yet :-D But, for easier comparison, here's just the maximum numbers side by side by side:
 That 14.8C drop on the Mem1 though :-D I have thought about getting Fujipoly again, but because I can't find 2mm pads from them, I'd have to order double what I need in 1mm and that would get expensive fast. Not to mention apparently Fuji extreme has 17W/mK but Thermal Grizzly Kryonaut is only around 12W/mK - so in theory, doing the cheaper 12W pads should be about as good as it's gonna get. I'm just glad I apparently done need to clean that paste off... at least not anytime soon. I would say the paste isn't totally worth it overall, but that 2.5C drop on Mem1 from pads to paste, without all the memory even having the higher quality pads on it, is pretty good... and, as some have pointed out, doing paste makes the heatsinks very much less likely to move around, vs pads (though tape is best, it also performs thermally the worst). I should've included the taped heatsinks only numbers in those charts. Ah well.
Are your heat sinks cool to the touch close to the end of the run the tall ones i have are a lot cooler than the short ones im wondering if the sinks are heat soaking also? There is a surprising large amount of heat that comes off the back of these cards! The 12w/mk 2mm thermo grizzly is the stuff im using with no backplate the heatsink thats closest to the pcie slot on mine is still warm to the touch even with a 2500 rpm fan right on top of it. I wonder how much the temps would drop if the center pad on the back of the die was taken out. even my 36mm tall heat sink is warm. the front one is only on the outer most vram is cool to the touch. Not sure those have a sensor in them.
|
DZelmer
Superclocked Member
- Total Posts : 219
- Reward points : 0
- Joined: 2014/11/06 00:37:01
- Status: offline
- Ribbons : 0
Re: 3090 (Kingpin & others!) - Get that backside VRAM cool!
2021/02/28 01:21:26
(permalink)
Dabadger84
DZelmer Do any of you have a 3090 along with the kingpin? if so do the back plates have the screw holes in the same spots?
I had a 3090 FTW3 Hybrid, past tense, let me see if I can find a good shot of the backside of the GPU, mayhaps I can verify if the screw holes match...
Edit: Nope, because of the OLED display, they are different. Here's a shot of the HydroCopper version:
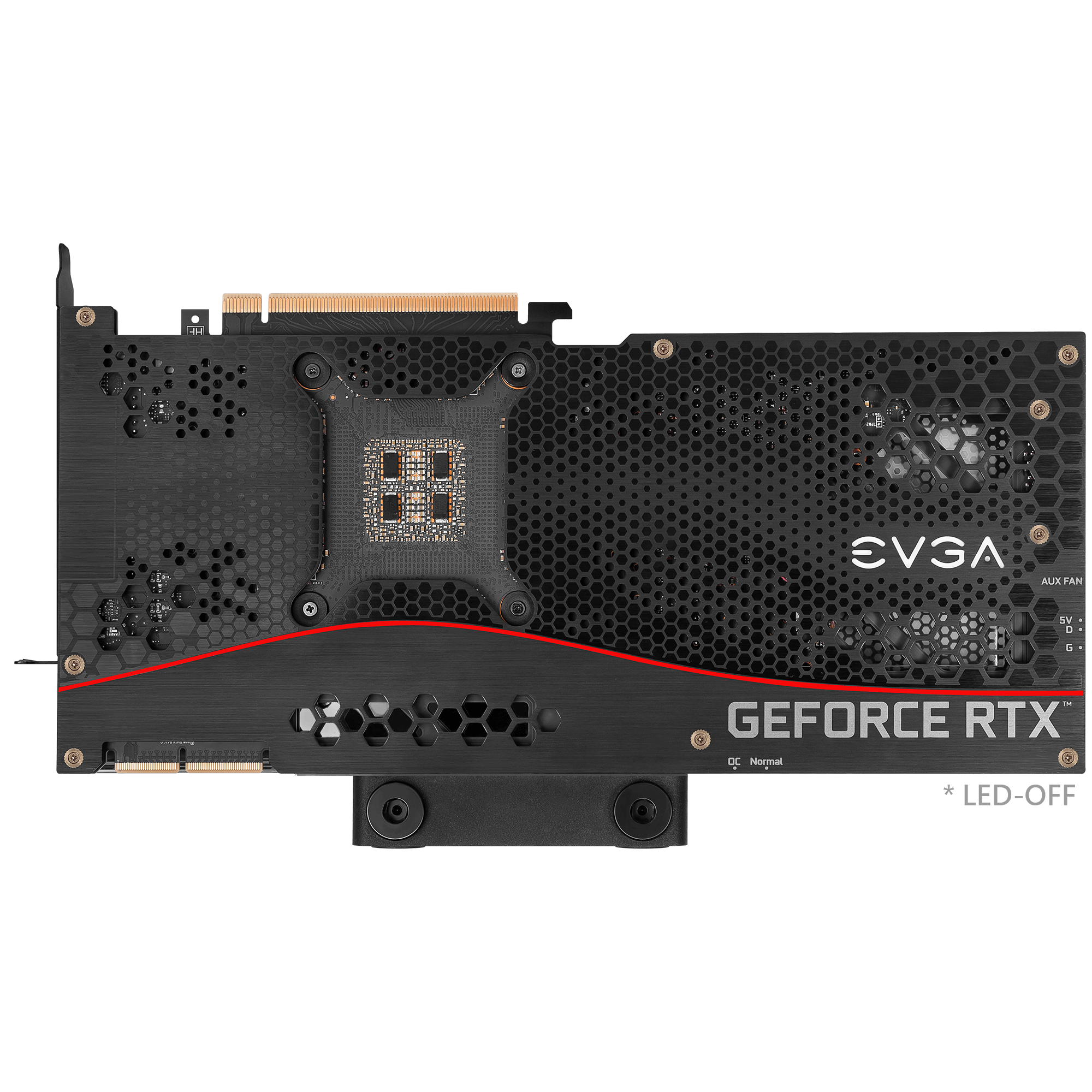 vs Kingpin:
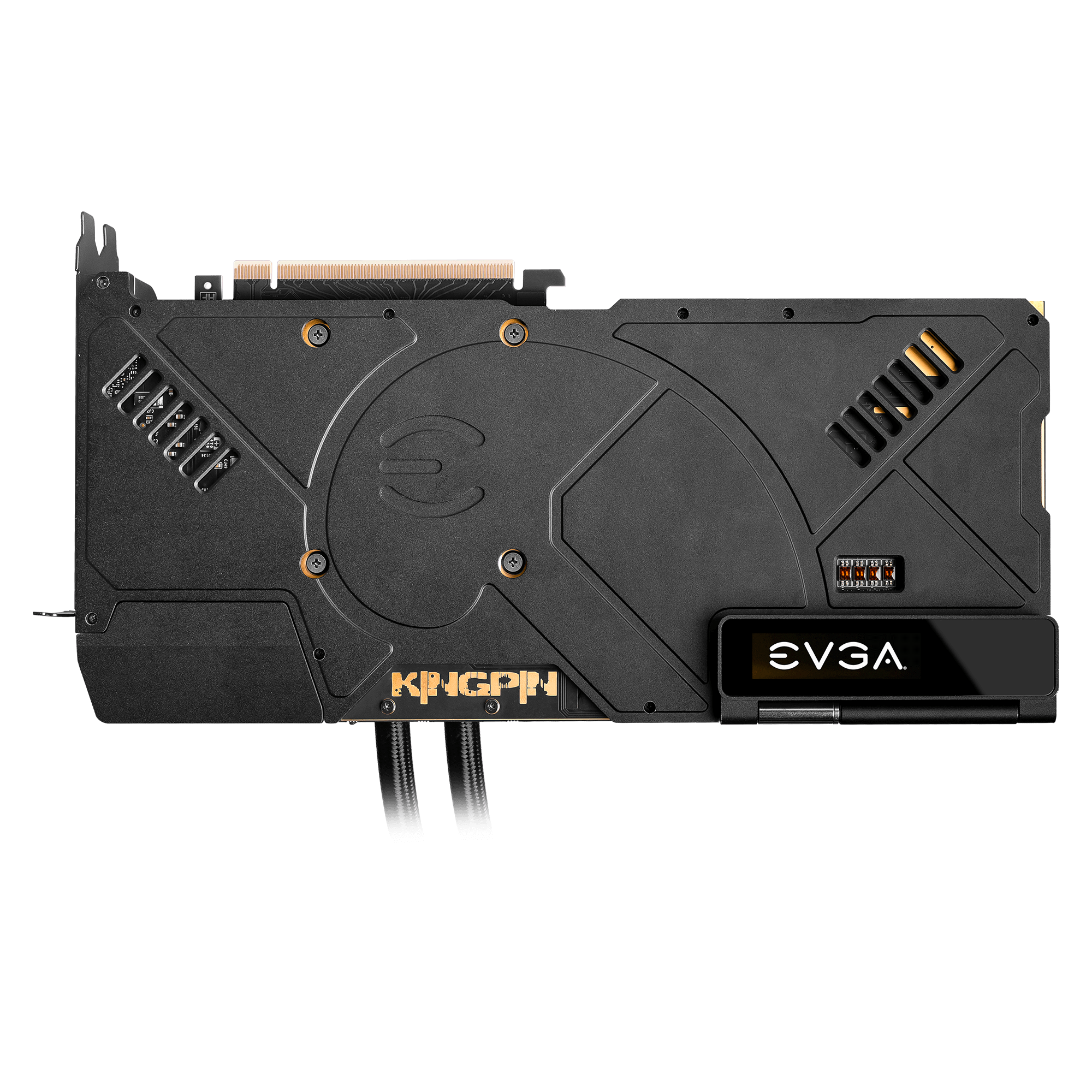
yep way way different was hoping the backplate i'm working on would fit other stuff also o well its a one card wonder! Thank you apricate that!
post edited by DZelmer - 2021/02/28 01:23:52
|
DZelmer
Superclocked Member
- Total Posts : 219
- Reward points : 0
- Joined: 2014/11/06 00:37:01
- Status: offline
- Ribbons : 0
Re: 3090 (Kingpin & others!) - Get that backside VRAM cool!
2021/02/28 01:35:07
(permalink)
Ok so upping my fan speed on the heat sinks from 2500 to 2900 maxed out 3k fan dropped mem1 3 deg and mem2 1 deg and i can repeat that just by changing the fan speed the temps change back and forth with fan speed after about 5 min they go up faster than down that for sure!
|
pclausen
Superclocked Member
- Total Posts : 197
- Reward points : 0
- Joined: 2017/07/22 20:02:38
- Status: offline
- Ribbons : 1

Re: 3090 (Kingpin & others!) - Get that backside VRAM cool!
2021/02/28 04:14:54
(permalink)
Dabadger84 What drivers are you using? Are you powering the fans off the GPU plug ins? I would highly recommend you get some of the splitters I use: https://www.ekwb.com/shop/ek-cable-splitter-4-fan-pwm-extended You can use those to power the fans directly off your PSU via 4-pin Molex, and still use PWM control via the GPU's radiator plugs, but no longer have to worry about the fan-draw effecting your power limit or causing other issues. I run mine off of my motherboard because the Z390 AORUS Master comes with thermocouples - I have those running to the radiator exhaust air on both the CPU & GPU radiators then the fan speed is adjusted based on that air temperature, so when the GPU or CPU are under load that causes the temperature of the radiator's exhaust air to increase, the fans speed up. This is especially nice because under lesser loads/bursty workloads, the fans don't spin up at all, because it's not enough heat generation to soak the radiator & increase the exhaust air temp.
I'm on the latest Nvidia drivers (461.72). I have a total of 12 fans on my rig (excluding the single KingPin GPU fan). All fans are controlled from my Lian Li L-Connect that has the ability to control up to 16 fans. It came with my SL120 Uni Fans. I have 4 of those on my 480 rad in push mode. The Uni fans snap together for both PWM power and RGB LEDs, so only a single pair of wires go between the L-Connect and those 4 fans. The 3 + 3 Noctua fans on the 360 KingPin rad are connected to the L-Connect as well via a pair of these: The fan blowing on the KingPin rear plate (and 2nd fan blowing across my PCIe 4.0 NVMe's and 25 Gbps NIC, is connected to the 4th bank. So overall it looks like this: I don't really like the L-Connect controller since when I switch to PWM mode for any of the 4 banks, the fans all run at 100% which I don't want, so I run all 4 banks in manual mode at modest speeds except when trying a PR high scores. :) And of course I get none of the benefits of the fans only spinning up when things heat up. I was running all the fans off my Asus ROG Crosshair VIII Formula, but I despise the Asus AI Suite 3 for controlling them. It does provide a lot of fan headers though: 1. W_PUMP+ (my EK D5 pump is connected to it) 2. AIO Pump 3. CPU Fan 4. Chassis Fan 1 5. Chassis Fan 2 6. Chassis Fan 3 7. High Amp Fan The mobo also has headers for water temp and flow, but again, I just hate being stuck with the AI Suite for controlling things. Once I'm 100% on water, I plan to use my Aquacomputer aquero 6 controller to run the entire show. However, it requires a 5 1/4" bay, which my Thermaltake Core P5 does not have, which is the main reason I'm not using it right now. I used that controller for 2 years on my 4x MSI 1080Ti SeaHawk EK rig and it was awesome. That was all mounted in my Thermaltake Core X9 snow edition monster chassis. I was running dual 480 rads along with a 240 in it, keeping those 1080Ti nice and cool. It just looks a little dated now. I was looking at the View 91 like you have, and while it does have 5 1/4" bays on the front, I don't think I would be able to use any of them with 480 rads. What do you think since you own one? Sorry for getting this thread completely off the rails... :)
|
Frammish
Superclocked Member
- Total Posts : 236
- Reward points : 0
- Joined: 2014/10/18 15:24:44
- Status: offline
- Ribbons : 0
Re: 3090 (Kingpin & others!) - Get that backside VRAM cool!
2021/02/28 06:38:26
(permalink)
I didn’t read the full thread so apologies if this was already mentioned/discovered, but there is a measurement technique for evaluating bearing clearances that uses a precision thread of material that spreads out under compression and the width of the deformed thread tells you the clearance thickness (Plastigauge). Chip clearance measurements are much bigger but you can use a little ball of Play-Doh sandwiched with plastic wrap (so it doesn’t stick to anything) placed on chips you want to measure, mount the back plate or heat sink, take it back apart, and carefully measure the thicknesses using a micrometer. You can then add however much squish you want and go with that.
|
Drunk_Chicken
New Member
- Total Posts : 2
- Reward points : 0
- Joined: 2013/12/19 16:30:51
- Status: offline
- Ribbons : 0
Re: 3090 (Kingpin & others!) - Get that backside VRAM cool!
2021/02/28 09:52:40
(permalink)
Bit of an odd question, but I just completed this mod and been having it reach thermal equilibrium via mining. My temps on the iCX sensors are ~8-10c lower, but memory junction has now gone up from ~94c max to 100-102c max. Does junction read from the front chips and I somehow wiggled a pad loose? Or do y'all think I need a fan over the backplate heatsinks now since its heatsoaking? Any help would be appreciated, this has got me stumped. EDIT: Would the torque on the backplate screws (mounting pressure) affect this in anyway y'all think? Too much, too little, etc
post edited by Drunk_Chicken - 2021/02/28 09:59:07
|
DZelmer
Superclocked Member
- Total Posts : 219
- Reward points : 0
- Joined: 2014/11/06 00:37:01
- Status: offline
- Ribbons : 0
Re: 3090 (Kingpin & others!) - Get that backside VRAM cool!
2021/02/28 09:55:59
(permalink)
Frammish I didn’t read the full thread so apologies if this was already mentioned/discovered, but there is a measurement technique for evaluating bearing clearances that uses a precision thread of material that spreads out under compression and the width of the deformed thread tells you the clearance thickness (Plastigauge). Chip clearance measurements are much bigger but you can use a little ball of Play-Doh sandwiched with plastic wrap (so it doesn’t stick to anything) placed on chips you want to measure, mount the back plate or heat sink, take it back apart, and carefully measure the thicknesses using a micrometer. You can then add however much squish you want and go with that.
Already ahead of you on that one I'm very familiar with plastiguage i have also used solder for checking clearances along with modeling clay and yes i have even done palydough. Good idea regardless we are currently working on getting a initial drawing and cam program to make a nice flat back plate and if the guy doing the cam program is willing to let me get real fancy try and make all the clearances for the vram chips to 1mm or less. The vrm clearances already seem to be .5mm or less.
|
Dabadger84
CLASSIFIED Member
- Total Posts : 3426
- Reward points : 0
- Joined: 2018/05/11 23:49:52
- Location: de_Overpass, USA
- Status: offline
- Ribbons : 10

Re: 3090 (Kingpin & others!) - Get that backside VRAM cool!
2021/02/28 10:14:39
(permalink)
DZelmer Ok so upping my fan speed on the heat sinks from 2500 to 2900 maxed out 3k fan dropped mem1 3 deg and mem2 1 deg and i can repeat that just by changing the fan speed the temps change back and forth with fan speed after about 5 min they go up faster than down that for sure!
I may try a 100% fan speed run, just to see how it goes - the runs I've done so far have been with a consistent fan speed on the GPU radiator & GPU backplate heatsink fan speed, but not 100% speed. Now that the heatsinks are mostly, 6 of the 11 are thermal pasted on, other 5 are taped cuz they're on VRMs, I would assume they're getting more heat to transfer out, as indicated by the drop in temps. I'm going to get some 12W or 17W/mK pads for the VRAM on the backplate side eventually, the individual chip & 3-chip set already have 12.8W/mK pads on them, just the other two sets still have 6W/mK. I really want to take the face side apart & redo that stuff, has anyone done that and if so, what did you use to clean the puddy off/what size pads are needed to replace that, I assume 3mm since I recall eVGA saying it's 2.85mm from VRMs to heatsink on a Hybrid card, or something like that. I was going to pick up some Fujipoly for the VRAM for sure, until I remembered I'd have to double stack the 1mm pads, which means I'd have to buy 2 sheets of 60 x 50 x 1mm to do all of the VRAM that isn't already under better than 6W pads - that's over $50 more in pads, just to do the two RAM sections. Not sure the drop in temps would be worth that cost. I'm just glad the $14 tube of thermal paste I completely used on the backplate actually showed improvement over the thermal pads being on the backpalte lol that would've been very depressing otherwise to have to clean that off knowing it was a complete waste.
ModRigs: https://www.modsrigs.com/detail.aspx?BuildID=42891 Specs:5950x @ 4.7GHz 1.3V - Asus Crosshair VIII Hero - eVGA 1200W P2 - 4x8GB G.Skill Trident Z Royal Silver @ 3800 CL14Gigabyte RTX 4090 Gaming OC w/ Core: 2850MHz @ 1000mV, Mem: +1500MHz - Samsung Odyssey G9 49" Super-Ultrawide 240Hz Monitor
|
Dabadger84
CLASSIFIED Member
- Total Posts : 3426
- Reward points : 0
- Joined: 2018/05/11 23:49:52
- Location: de_Overpass, USA
- Status: offline
- Ribbons : 10

Re: 3090 (Kingpin & others!) - Get that backside VRAM cool!
2021/02/28 10:26:14
(permalink)
pclausen
Dabadger84 What drivers are you using? Are you powering the fans off the GPU plug ins? I would highly recommend you get some of the splitters I use: https://www.ekwb.com/shop/ek-cable-splitter-4-fan-pwm-extended You can use those to power the fans directly off your PSU via 4-pin Molex, and still use PWM control via the GPU's radiator plugs, but no longer have to worry about the fan-draw effecting your power limit or causing other issues. I run mine off of my motherboard because the Z390 AORUS Master comes with thermocouples - I have those running to the radiator exhaust air on both the CPU & GPU radiators then the fan speed is adjusted based on that air temperature, so when the GPU or CPU are under load that causes the temperature of the radiator's exhaust air to increase, the fans speed up. This is especially nice because under lesser loads/bursty workloads, the fans don't spin up at all, because it's not enough heat generation to soak the radiator & increase the exhaust air temp.
I'm on the latest Nvidia drivers (461.72). I have a total of 12 fans on my rig (excluding the single KingPin GPU fan). All fans are controlled from my Lian Li L-Connect that has the ability to control up to 16 fans. It came with my SL120 Uni Fans. I have 4 of those on my 480 rad in push mode. The Uni fans snap together for both PWM power and RGB LEDs, so only a single pair of wires go between the L-Connect and those 4 fans. The 3 + 3 Noctua fans on the 360 KingPin rad are connected to the L-Connect as well via a pair of these: The fan blowing on the KingPin rear plate (and 2nd fan blowing across my PCIe 4.0 NVMe's and 25 Gbps NIC, is connected to the 4th bank. So overall it looks like this: I don't really like the L-Connect controller since when I switch to PWM mode for any of the 4 banks, the fans all run at 100% which I don't want, so I run all 4 banks in manual mode at modest speeds except when trying a PR high scores. :) And of course I get none of the benefits of the fans only spinning up when things heat up. I was running all the fans off my Asus ROG Crosshair VIII Formula, but I despise the Asus AI Suite 3 for controlling them. It does provide a lot of fan headers though: 1. W_PUMP+ (my EK D5 pump is connected to it) 2. AIO Pump 3. CPU Fan 4. Chassis Fan 1 5. Chassis Fan 2 6. Chassis Fan 3 7. High Amp Fan The mobo also has headers for water temp and flow, but again, I just hate being stuck with the AI Suite for controlling things. Once I'm 100% on water, I plan to use my Aquacomputer aquero 6 controller to run the entire show. However, it requires a 5 1/4" bay, which my Thermaltake Core P5 does not have, which is the main reason I'm not using it right now. I used that controller for 2 years on my 4x MSI 1080Ti SeaHawk EK rig and it was awesome. That was all mounted in my Thermaltake Core X9 snow edition monster chassis. I was running dual 480 rads along with a 240 in it, keeping those 1080Ti nice and cool. It just looks a little dated now. I was looking at the View 91 like you have, and while it does have 5 1/4" bays on the front, I don't think I would be able to use any of them with 480 rads. What do you think since you own one? Sorry for getting this thread completely off the rails... :)
Nah it's all good, we learnin' together. That's one thing I will compliment Gigabyte on, their software isn't very bloaty, and their control stuff for fans, which interfaces with BIOS but can be set separately from it, is a "set and close" type application. And it is automatic, doesn't have to be loaded every start up - that's what controls all of my fans except the GPU on board fan & the 4 Thermaltakes I still have in the system - which those are all just M.2 or intake/exhaust on the case, so they're just at 50% or 70% on the intakes. GPU radiator fans idle at ~950RPM to keep the dust build up at idle to a minimum, and they ramp up to around 2000RPM under heavy heavy loads (all EK Vardar fans, so they do get noticeably loudish at 2000RPM), depending on the GPU radiator air exhaust temp. CPU radiator fans I have all set to control based on CPU temperature right now, along with the CPU loop pump, if the CPU doesn't go over 50C, they stay pretty calm. I still gotta work out the kinks on those fan steps, with all this messing around with the Kingpin & stuff I haven't had time to fine tune the loop since I installed it, and given that I'm going to have to take it apart for a CPU block swap (and adding the 480mm radiator that's coming soon), I figure I can just wait to do that. But SIV (Gigabyte's fan control software that does other things as well) is a pretty decent all in one type thing. It's very bloaty when it's loaded & you're changing stuff in it, but once you close it it's like it's gone but still controlling fans etc. That's an example of my GPU radiator steps, from back when I had a 3090 FTW3 Hybrid with the stock fans still on it so the RPM readouts are different. You click the case on the left & tell it what temperature you want to control that fan header based on, the only one you cannot change, of course, is the main CPU header, that is always controlled by CPU, and that's where I have the CPU pump plugged in to now. I'm kinda curious how the mono-pad I had on before will perform now that I have the thermal paste on the other side of the backplate. Might swap that out again, see how it goes, for the lulz. I'm trying not to overdo swapping the pads over & over again because every time I swap them, even though I have gloves on, they still get fuzzies & stuff. The mono-pad I've been fortunate enough to not get dirty much, yet: I might swap it back in tonight, see how it does. I wish I could get that much Fujipoly, but that'd be like $200 worth of thermal pads. lol
ModRigs: https://www.modsrigs.com/detail.aspx?BuildID=42891 Specs:5950x @ 4.7GHz 1.3V - Asus Crosshair VIII Hero - eVGA 1200W P2 - 4x8GB G.Skill Trident Z Royal Silver @ 3800 CL14Gigabyte RTX 4090 Gaming OC w/ Core: 2850MHz @ 1000mV, Mem: +1500MHz - Samsung Odyssey G9 49" Super-Ultrawide 240Hz Monitor
|
Dabadger84
CLASSIFIED Member
- Total Posts : 3426
- Reward points : 0
- Joined: 2018/05/11 23:49:52
- Location: de_Overpass, USA
- Status: offline
- Ribbons : 10

Re: 3090 (Kingpin & others!) - Get that backside VRAM cool!
2021/02/28 10:31:25
(permalink)
Drunk_Chicken Bit of an odd question, but I just completed this mod and been having it reach thermal equilibrium via mining. My temps on the iCX sensors are ~8-10c lower, but memory junction has now gone up from ~94c max to 100-102c max. Does junction read from the front chips and I somehow wiggled a pad loose? Or do y'all think I need a fan over the backplate heatsinks now since its heatsoaking? Any help would be appreciated, this has got me stumped. EDIT: Would the torque on the backplate screws (mounting pressure) affect this in anyway y'all think? Too much, too little, etc
I don't think backplate screws being loose would effect it very much, they're kind of hard to leave "lose", you don't want to overtighten them & strip the screws either. Are you sure you have good contact on all the pads on the backplate side of the card? Your junction temp definitely shouldn't have went up, unless something on the die-side came loose. DZelmer
Frammish I didn’t read the full thread so apologies if this was already mentioned/discovered, but there is a measurement technique for evaluating bearing clearances that uses a precision thread of material that spreads out under compression and the width of the deformed thread tells you the clearance thickness (Plastigauge). Chip clearance measurements are much bigger but you can use a little ball of Play-Doh sandwiched with plastic wrap (so it doesn’t stick to anything) placed on chips you want to measure, mount the back plate or heat sink, take it back apart, and carefully measure the thicknesses using a micrometer. You can then add however much squish you want and go with that.
Already ahead of you on that one I'm very familiar with plastiguage i have also used solder for checking clearances along with modeling clay and yes i have even done palydough. Good idea regardless we are currently working on getting a initial drawing and cam program to make a nice flat back plate and if the guy doing the cam program is willing to let me get real fancy try and make all the clearances for the vram chips to 1mm or less. The vrm clearances already seem to be .5mm or less.
Yeah the VRM power stages or whatever the backside boxes are already squishy in to even 1.5mm pads a fair bit, and 2mm they get very indented, so I imagine with a little resizing you can get them pretty close indeed. It would be really cool to get super close to the VRAM so it only needs .5mm pads, then have the backplate thinner, with an option to do heatsinks or have it be a block, but we'll see eh?
ModRigs: https://www.modsrigs.com/detail.aspx?BuildID=42891 Specs:5950x @ 4.7GHz 1.3V - Asus Crosshair VIII Hero - eVGA 1200W P2 - 4x8GB G.Skill Trident Z Royal Silver @ 3800 CL14Gigabyte RTX 4090 Gaming OC w/ Core: 2850MHz @ 1000mV, Mem: +1500MHz - Samsung Odyssey G9 49" Super-Ultrawide 240Hz Monitor
|
rangerscott
iCX Member
- Total Posts : 348
- Reward points : 0
- Joined: 2008/04/27 20:31:40
- Location: USA
- Status: offline
- Ribbons : 2
Re: 3090 (Kingpin & others!) - Get that backside VRAM cool!
2021/02/28 11:29:11
(permalink)
Paste will always out do pads and the only reason it wouldnt is because of poor contact.
12900k Z690 Dark 7900 XTX Nitro 32gb Trident z5 @ 6000 Corsair RM1000X psu
|
rangerscott
iCX Member
- Total Posts : 348
- Reward points : 0
- Joined: 2008/04/27 20:31:40
- Location: USA
- Status: offline
- Ribbons : 2
Re: 3090 (Kingpin & others!) - Get that backside VRAM cool!
2021/02/28 11:30:13
(permalink)
Been thinking of the mp5works but seeing as its $144 to get to me, Im just gonna get a cheap full cover block and make my own backplate heat transferer.
For that much I'd want it to be bigger or actually become the backplate.
12900k Z690 Dark 7900 XTX Nitro 32gb Trident z5 @ 6000 Corsair RM1000X psu
|
Dabadger84
CLASSIFIED Member
- Total Posts : 3426
- Reward points : 0
- Joined: 2018/05/11 23:49:52
- Location: de_Overpass, USA
- Status: offline
- Ribbons : 10

Re: 3090 (Kingpin & others!) - Get that backside VRAM cool!
2021/02/28 12:27:09
(permalink)
rangerscott Paste will always out do pads and the only reason it wouldnt is because of poor contact.
Well according to Kryonaut's page, it's transfer rate is 12.6W/mK - so Fuji's 17W pads should perform better, but, I would just want the pads for better transfer from the stuff to the backplate, I'm not taking that paste off the backplate without a really good reason to lol I'll probably get more of the Thermalright 12.8W/mK pads, do the other VRAM chips that don't already have that on them, and leave it at that.
ModRigs: https://www.modsrigs.com/detail.aspx?BuildID=42891 Specs:5950x @ 4.7GHz 1.3V - Asus Crosshair VIII Hero - eVGA 1200W P2 - 4x8GB G.Skill Trident Z Royal Silver @ 3800 CL14Gigabyte RTX 4090 Gaming OC w/ Core: 2850MHz @ 1000mV, Mem: +1500MHz - Samsung Odyssey G9 49" Super-Ultrawide 240Hz Monitor
|
DZelmer
Superclocked Member
- Total Posts : 219
- Reward points : 0
- Joined: 2014/11/06 00:37:01
- Status: offline
- Ribbons : 0
Re: 3090 (Kingpin & others!) - Get that backside VRAM cool!
2021/02/28 12:39:34
(permalink)
rangerscott Been thinking of the mp5works but seeing as its $144 to get to me, Im just gonna get a cheap full cover block and make my own backplate heat transferer.
For that much I'd want it to be bigger or actually become the backplate.
Yep thats why im going to make a back plate i would love to make it so it can be water cooled also but we shall see how it come out initially
|
Dabadger84
CLASSIFIED Member
- Total Posts : 3426
- Reward points : 0
- Joined: 2018/05/11 23:49:52
- Location: de_Overpass, USA
- Status: offline
- Ribbons : 10

Re: 3090 (Kingpin & others!) - Get that backside VRAM cool!
2021/02/28 13:59:15
(permalink)
DZelmer
rangerscott Been thinking of the mp5works but seeing as its $144 to get to me, Im just gonna get a cheap full cover block and make my own backplate heat transferer.
For that much I'd want it to be bigger or actually become the backplate.
Yep thats why im going to make a back plate i would love to make it so it can be water cooled also but we shall see how it come out initially
Yeah I would go for a nice thin copper backplate with good contact spacing first, then maybe see about doing a G 1/4 fitting backplate block... it would be nice if someone actually designed a block that did both, but fitting that would be... not impossible, but it would require assembly as you're applying things, would not be easy.
ModRigs: https://www.modsrigs.com/detail.aspx?BuildID=42891 Specs:5950x @ 4.7GHz 1.3V - Asus Crosshair VIII Hero - eVGA 1200W P2 - 4x8GB G.Skill Trident Z Royal Silver @ 3800 CL14Gigabyte RTX 4090 Gaming OC w/ Core: 2850MHz @ 1000mV, Mem: +1500MHz - Samsung Odyssey G9 49" Super-Ultrawide 240Hz Monitor
|
rangerscott
iCX Member
- Total Posts : 348
- Reward points : 0
- Joined: 2008/04/27 20:31:40
- Location: USA
- Status: offline
- Ribbons : 2
Re: 3090 (Kingpin & others!) - Get that backside VRAM cool!
2021/02/28 14:01:25
(permalink)
I got response back from mp5 on youtube. They say its big enough but arent there more hot stuff farther down on non FE models?
12900k Z690 Dark 7900 XTX Nitro 32gb Trident z5 @ 6000 Corsair RM1000X psu
|
Clovis559
SSC Member
- Total Posts : 563
- Reward points : 0
- Joined: 2020/09/18 13:53:08
- Status: offline
- Ribbons : 3
Re: 3090 (Kingpin & others!) - Get that backside VRAM cool!
2021/02/28 16:23:17
(permalink)
Dabadger84
rangerscott Paste will always out do pads and the only reason it wouldnt is because of poor contact.
Well according to Kryonaut's page, it's transfer rate is 12.6W/mK - so Fuji's 17W pads should perform better, but, I would just want the pads for better transfer from the stuff to the backplate, I'm not taking that paste off the backplate without a really good reason to lol I'll probably get more of the Thermalright 12.8W/mK pads, do the other VRAM chips that don't already have that on them, and leave it at that.
I need to check out those pads, I just got caught up on this whole thread. You are going mad and I like it! I have a lil project going too for the front side VRMs... You got that much spread out of 1.5g? When are you just going to take the backplate off? O.o
|
Dabadger84
CLASSIFIED Member
- Total Posts : 3426
- Reward points : 0
- Joined: 2018/05/11 23:49:52
- Location: de_Overpass, USA
- Status: offline
- Ribbons : 10

Re: 3090 (Kingpin & others!) - Get that backside VRAM cool!
2021/02/28 17:26:37
(permalink)
Clovis559
Dabadger84
rangerscott Paste will always out do pads and the only reason it wouldnt is because of poor contact.
Well according to Kryonaut's page, it's transfer rate is 12.6W/mK - so Fuji's 17W pads should perform better, but, I would just want the pads for better transfer from the stuff to the backplate, I'm not taking that paste off the backplate without a really good reason to lol I'll probably get more of the Thermalright 12.8W/mK pads, do the other VRAM chips that don't already have that on them, and leave it at that.
I need to check out those pads, I just got caught up on this whole thread. You are going mad and I like it! I have a lil project going too for the front side VRMs... You got that much spread out of 1.5g? When are you just going to take the backplate off? O.o
I did. Some temps were not better at all and only one was significantly better, so I put it back on. And yeah, I could've gotten more, but I decided to fill in the groves. I regret that decision, but then again, I really didn't need to spread it any further. It was pretty thin but the time I got done with it, I mostly used the applicator that came with the tube, but I did use my finger on some areas, so some of it ended up on my glove. Currently plan is to just redo the other memory with higher heat transfer pads, and then call it good. The nearly -15 and nearly -10C drops on the two Mem temps is quite good - I just wish I'd went this way to begin with & saved the money, but at least this is an experiment I don't really have to repeat, next time I do this to a card, I'll know to just get higher W/mK pads, a thing of thermal paste & some heatsinks & then have a party. lol I wish I could justify the Fujipoly, but after seeing that Thermal Grizzly only has about the same heat transference rating as the Thermalright pads I'm going to put more of on the memory when I can, I don't see the point in spending $70 on JUST more pads to redo all the memory with 17W/mK pads, when that performance will still be gimped elsewhere. Maybe when/if I redo the face/die side of the card, I'll get some Fuji for the Memory on that side. Speaking of that, what size pads did you use on the memory when you redid yours on the face-side? 1mm? I forget.
ModRigs: https://www.modsrigs.com/detail.aspx?BuildID=42891 Specs:5950x @ 4.7GHz 1.3V - Asus Crosshair VIII Hero - eVGA 1200W P2 - 4x8GB G.Skill Trident Z Royal Silver @ 3800 CL14Gigabyte RTX 4090 Gaming OC w/ Core: 2850MHz @ 1000mV, Mem: +1500MHz - Samsung Odyssey G9 49" Super-Ultrawide 240Hz Monitor
|
Dabadger84
CLASSIFIED Member
- Total Posts : 3426
- Reward points : 0
- Joined: 2018/05/11 23:49:52
- Location: de_Overpass, USA
- Status: offline
- Ribbons : 10

Re: 3090 (Kingpin & others!) - Get that backside VRAM cool!
2021/02/28 18:17:32
(permalink)
ModRigs: https://www.modsrigs.com/detail.aspx?BuildID=42891 Specs:5950x @ 4.7GHz 1.3V - Asus Crosshair VIII Hero - eVGA 1200W P2 - 4x8GB G.Skill Trident Z Royal Silver @ 3800 CL14Gigabyte RTX 4090 Gaming OC w/ Core: 2850MHz @ 1000mV, Mem: +1500MHz - Samsung Odyssey G9 49" Super-Ultrawide 240Hz Monitor
|
DZelmer
Superclocked Member
- Total Posts : 219
- Reward points : 0
- Joined: 2014/11/06 00:37:01
- Status: offline
- Ribbons : 0
Re: 3090 (Kingpin & others!) - Get that backside VRAM cool!
2021/02/28 22:55:42
(permalink)
Well i took the pad off the back of the die and it didn't change the temps any well half a deg up or dawn probably about the same if i ran the test 5 times they would all be up or down that much.... guess there isn't much heat coming through the board.
|
ShadowMAN280x
New Member
- Total Posts : 19
- Reward points : 0
- Joined: 2013/11/25 09:50:01
- Status: offline
- Ribbons : 0
Re: 3090 (Kingpin & others!) - Get that backside VRAM cool!
2021/03/01 03:28:20
(permalink)
Question: Can you explain what extra coverage you gain by redoing backside thermal pads? Do stock thermal pads really need to be changed? I ask because I'm considering just using stock thermal pads, paste on backplate, heatsinks, and 80mm fan.
post edited by ShadowMAN280x - 2021/03/01 05:14:13
|
Clovis559
SSC Member
- Total Posts : 563
- Reward points : 0
- Joined: 2020/09/18 13:53:08
- Status: offline
- Ribbons : 3
Re: 3090 (Kingpin & others!) - Get that backside VRAM cool!
2021/03/01 10:31:18
(permalink)
ShadowMAN280x Question: Can you explain what extra coverage you gain by redoing backside thermal pads? Do stock thermal pads really need to be changed? I ask because I'm considering just using stock thermal pads, paste on backplate, heatsinks, and 80mm fan.
Originally only the GPU and the memory has thermal pads. They have added to the backside of the VRMS.
|
Dabadger84
CLASSIFIED Member
- Total Posts : 3426
- Reward points : 0
- Joined: 2018/05/11 23:49:52
- Location: de_Overpass, USA
- Status: offline
- Ribbons : 10

Re: 3090 (Kingpin & others!) - Get that backside VRAM cool!
2021/03/01 10:41:58
(permalink)
ShadowMAN280x Question: Can you explain what extra coverage you gain by redoing backside thermal pads? Do stock thermal pads really need to be changed? I ask because I'm considering just using stock thermal pads, paste on backplate, heatsinks, and 80mm fan.
The problem is if you take the backplate off, at all, you're probably going to damage the stock pads on the backplate side, that's part of why I replaced them. They're the kind that rip the first time you attempt to remove them unless you're gentle - and the amount of force required to remove the backplate has a high chance of ripping them, because of the sticky box that's towards the OLED end of the card under the backplate that's holding it on. I would also recommend doing pads on the VRMs, as that does have an effect on temps. Just doing paste & heatsinks on the backplate will still positively effect temps, but it won't be as dramatic a drop... and the stock pad on the back of the die is pretty small. Edit: Got confirmation EK is sending a replacement CPU block out to me ^_^ dunno when it'll be here, maybe sometime this week, I hope.
ModRigs: https://www.modsrigs.com/detail.aspx?BuildID=42891 Specs:5950x @ 4.7GHz 1.3V - Asus Crosshair VIII Hero - eVGA 1200W P2 - 4x8GB G.Skill Trident Z Royal Silver @ 3800 CL14Gigabyte RTX 4090 Gaming OC w/ Core: 2850MHz @ 1000mV, Mem: +1500MHz - Samsung Odyssey G9 49" Super-Ultrawide 240Hz Monitor
|